Opening Success: Casting Aluminum Made Easy
Opening Success: Casting Aluminum Made Easy
Blog Article
Aluminum Spreading Providers Revealed: Essential Insights and Tips
Discovering the world of aluminum spreading services can unveil a world of elaborate procedures and nuanced considerations that are crucial for effective outcomes. As sectors progressively turn to light weight aluminum for its lightweight yet resilient buildings, comprehending the basics of casting ends up being extremely important. From the essential techniques to the complex information that can make or break a spreading task, there is a riches of understandings and tips waiting to be found. So, as we venture into the world of aluminum spreading solutions, prepare to uncover the crucial elements that can form the trajectory of your jobs and boost your understanding of this complex craft.
The Fundamentals of Light Weight Aluminum Casting
What essential processes are included in light weight aluminum spreading that create the foundation of this extensively used production technique? Aluminum casting is a versatile and affordable approach utilized in different markets to develop complex and intricate steel parts. The procedure begins with the melting of light weight aluminum ingots in a heating system, normally at temperature levels varying from 1220 ° F to 1670 ° F, depending on the particular aluminum alloy being made use of. As soon as molten, the aluminum is put right into a pre-designed mold and mildew tooth cavity, where it solidifies and takes the form of the mold and mildew.
After solidification, the mold and mildew is removed, and the casting goes through ending up procedures such as heat machining, surface area, and therapy finishing to satisfy the called for requirements. Recognizing these fundamental processes is necessary for attaining high-grade aluminum spreadings with mechanical buildings and precise measurements.
Various Casting Approaches Explained
Discovering the numerous strategies used in aluminum casting uses valuable understandings right into the varied approaches made use of to accomplish specific and complex steel elements. One common technique is sand casting, where a mold and mildew is produced utilizing compacted sand around a pattern of the preferred component. An additional approach, pass away casting, involves injecting liquified aluminum into a steel mold and mildew under high stress.
Aspects to Consider When Picking a Provider
When selecting an aluminum spreading company, reviewing their experience and experience is vital for making certain top quality and reliability in the manufacturing procedure. The copyright's experience in the area suggests their knowledge with different casting methods, prospective difficulties, and finest practices. It is important to make inquiries concerning the kinds of tasks they have dealt with in the past, guaranteeing they line up with the intricacy and specifications of your own project.
In addition, take into consideration the provider's reputation within the sector. Seek evaluations, testimonies, and study that show their capacity to deliver top notch aluminum castings regularly. A credible service provider will certainly frequently have certifications or affiliations Continue with market organizations, showcasing their commitment to excellence and adherence to sector standards.
Additionally, evaluate the copyright's capabilities in terms of modification, quantity needs, and task timelines. Guarantee that they can suit your particular requirements and have the flexibility to scale manufacturing as required. Efficient communication and openness pertaining to costs, preparation, and top quality control procedures are likewise crucial factors to consider when choosing a light weight aluminum spreading provider.
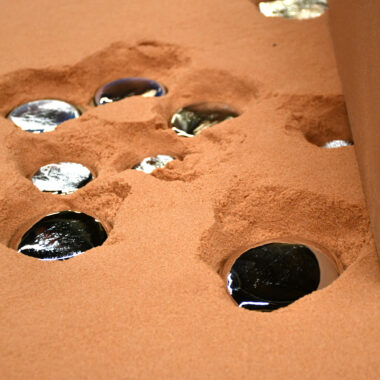
Typical Obstacles and Solutions
Navigating through the complexities of aluminum casting procedures commonly offers manufacturers with a collection of difficulties that call for ingenious services to make sure effectiveness and top quality in production. One usual challenge encountered in aluminum spreading is the formation of defects such as porosity, shrinkage, or incorporations as a result of inappropriate mold and mildew style or inadequate steel high quality. These issues can jeopardize the architectural honesty of the end product. To resolve this, manufacturers must perform complete simulations and examinations to maximize the spreading procedure parameters and make certain the top quality of the molds and materials used.
Another difficulty exists in attaining precise dimensional accuracy, specifically for complicated geometries. Variants in cooling down rates, mold development, and product residential properties can cause variances from the desired dimensions. Applying sophisticated modern technologies like computer-aided style (CAD) and computer system mathematical control (CNC) machining can boost accuracy and consistency in light weight aluminum casting. Additionally, keeping correct control over the melting and pouring procedures is vital to avoid problems like getting too hot or unequal circulation of the molten metal - casting aluminum. By buying automation and real-time tracking systems, producers can boost procedure control and minimize variants, inevitably improving the general high quality of aluminum cast items.
Tips for Optimizing Your Casting Projects
To boost the efficiency and high quality of your light weight aluminum casting projects, implementing calculated optimization methods is essential. One vital idea for enhancing your spreading projects is to thoroughly design the gating system. By ensuring that eviction system is properly designed and appropriately placed, you can boost the circulation of molten aluminum and minimize the possibilities of defects in the final casting. Additionally, utilizing computer simulations can help in predicting and examining the flow of steel during the spreading process, permitting adjustments to be made prior to real production begins.
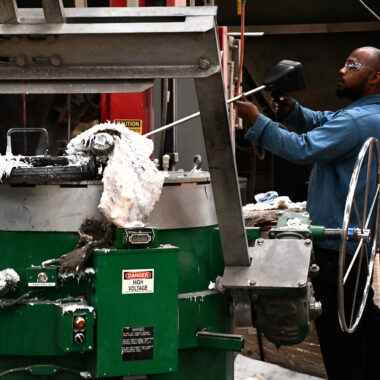
Verdict
To conclude, understanding the essentials of light weight aluminum spreading, various casting techniques, variables to take into consideration when selecting a copyright, usual challenges and remedies, and suggestions for enhancing casting tasks are necessary for successful results. By adhering to these understandings and implementing best companies, techniques and individuals can ensure reliable and efficient aluminum casting solutions that meet their details needs and needs.
Understanding these essential processes is crucial for achieving high-quality aluminum castings with precise dimensions and mechanical properties.
When choosing an aluminum spreading solution copyright, examining their experience and knowledge is crucial for guaranteeing high quality and reliability in the production procedure. Reliable interaction and transparency relating to expenses, lead times, and high quality control processes are also critical elements to take into consideration when selecting an aluminum casting solution copyright.
Navigating with the intricacies of aluminum casting procedures typically presents manufacturers with a series of obstacles that call for cutting-edge solutions to make certain efficiency and high quality in production. One usual obstacle dealt with in aluminum casting is the formation of problems such as porosity, shrinkage, or incorporations due to inappropriate mold design or poor metal quality.
Report this page